Min/Max Inventory Levels & Alerts
Ensure you always have the products your customers are looking for and remove “out of stock” from your vocabulary.
Know Exactly What To Order And When to Order
With Thrive Inventory you can bring together all of your different sales channels into our software making stock level management easy. With min/max inventory tracking and Alerts, you’ll know exactly what’s happening with all of your products at any set point in time, even if they are sold on different channels.
Min/Max Inventory Levels
- Notifications when a product reaches its minimum stock level
- Automatically add low stock products to Purchase Orders
- Generate Internal Transfers to replenish inventory levels
- Location-specific stock tracking and reporting
- View reporting based on minimum stock levels
- Create and edit min/max inventory levels with the Spreadsheet Bulk Upload Tool
Alerts
- Build Alerts based on product quantities, days of stock remaining, or categories like product name
- Receive an email notification when an Alert is triggered
- Location-specific
- Individual Alerts to the user
- Automatically generate Purchase Orders based on Alerts
- Set as many Alerts as you need
Why Businesses Choose Thrive Inventory Purchase Order Management
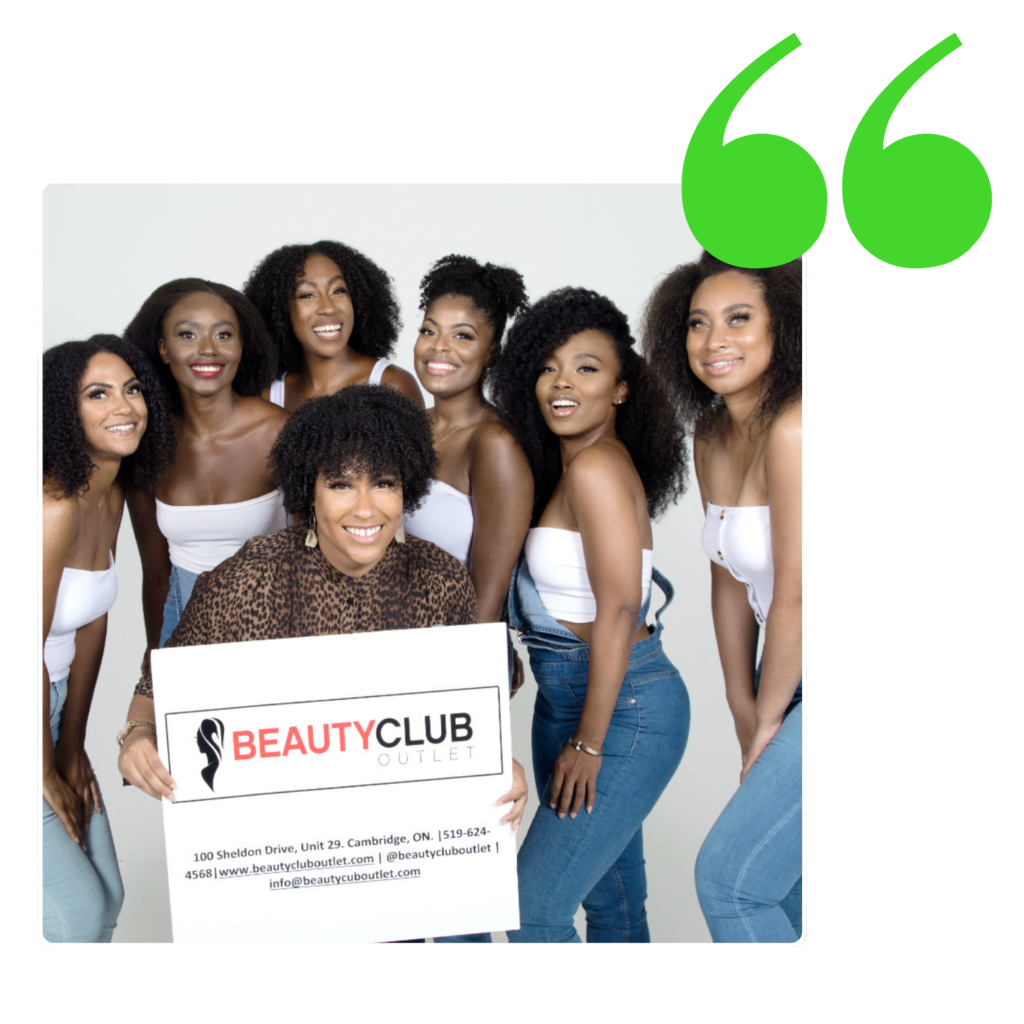
Meet Naomi, who opened a side business to serve Afro-textured customers. Four years later, Beauty Club Outlet became an international business by ditching Excel spreadsheets for Thrive Inventory.
When Beauty Club Outlet first opened, turning customers away due to stock-outs was common. Naomi and her team didn’t know what was on their shelves and the sell-through rate of products. Naomi used Min/Max Reorder Levels to easily create Purchase Orders which she emailed to vendors directly in Thrive Inventory, putting ordering on auto-pilot.
“If you run a product-based business, Thrive Inventory will increase your productivity tenfold. Would recommend 1000 times.”
- NAOMI, BEAUTY CLUB OUTLET
Why Businesses Choose Thrive Inventory Min/Max Inventory Levels
Min/Max Inventory Tracking Free For 30 Days
Join Thrive Inventory and start saving on average 1 hour per day per location. Get advanced features such as custom reporting, barcode scanning, automatic purchase orders, price tag printing and more.
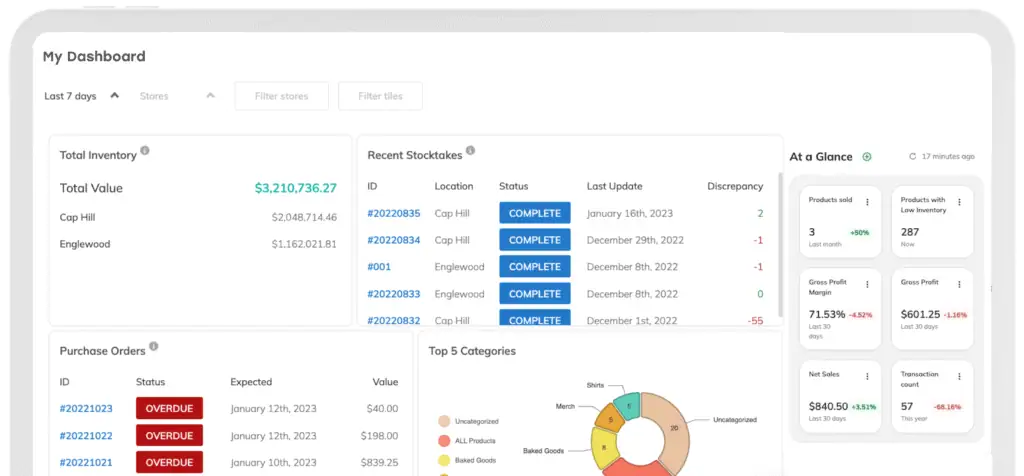
FAQs
What are Min/Max Levels?
Min/Max Levels, or periodic automatic replenishment (PAR) or reorder levels, define the minimum and maximum quantities you maintain for each item in your inventory. These thresholds help you manage stock efficiently, ensuring you always have enough product to meet demand while avoiding overstocking.
The minimum level represents the lowest quantity of a product you should have available to prevent running out, while the maximum level is the highest quantity you keep in stock to avoid unnecessary costs or excess inventory. They essentially tell you when and how much to reorder.
Setting Min/Max Levels is particularly valuable when your business experiences fluctuating demand, such as during holidays or major local events. They are also crucial for businesses handling perishable goods, like those in food and beverage, beauty, or hospitality, where precise inventory control helps reduce waste and maintain product quality.
Can Min/Max Levels and Alerts be set at the variant level?
Yes.
Can Min/Max Levels and Alerts be set for specific locations and sales channels?
Yes.
What type of Alerts can be set?
Alerts can be determined by quantity (less than or equal to) or days of stock remaining. Once you have set that condition, you can add specific categories, products, or variants.
How does the automatic Purchase Order generation work?
Automatically add low inventory products and products below their reorder point. Then review, approve, and send Purchase Orders directly to vendors in Thrive Inventory.
Auto-add Purchase Orders is available on Professional and up plans.
Are Min/Max Levels and Alerts set on the account-level or user-level?
Min/Max Levels are universal and are the same for everyone on the account. Alerts are specific to individual users.
What specific reports are available for products at or below Min/Max Levels?
The Low Inventory report is based on Alerts and Minimum Levels. Once a product quantity is at the Minimum Order Level, that item is included on the Low Inventory Report.